Learning Zone
Access all the fleet management tips, guides and insight you need for effective vehicle, maintenance, and workforce management.
Featured
The Power of Smart Data Integration
Discover how to simplify fleet data with smart integrations to drive faster, smarter decisions in this 20-minute webinar.
Read more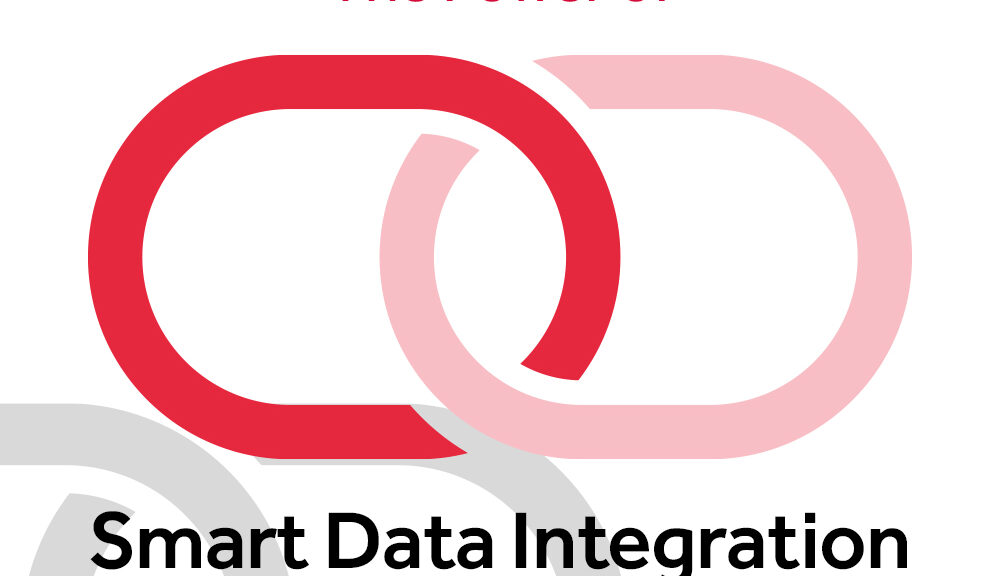
127 Assets
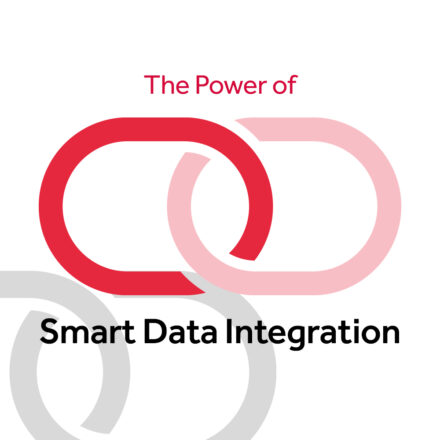
Learning Zone
The Power of Smart Data Integration
Read more
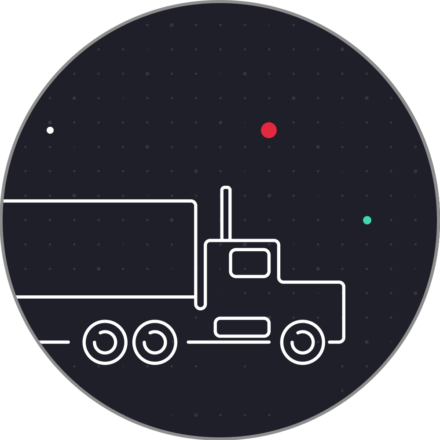
Learning Zone
Transforming Trucking with Fleet Management Software
Read more
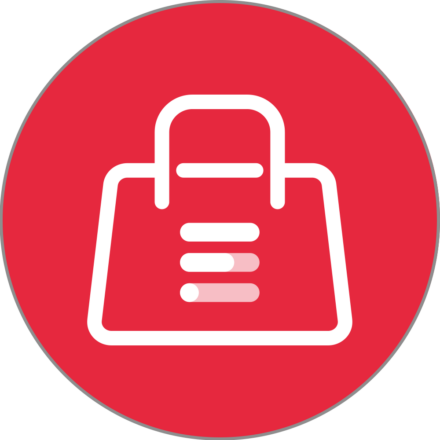
Learning Zone
Webinar: Introducing FleetWave Store
Read more
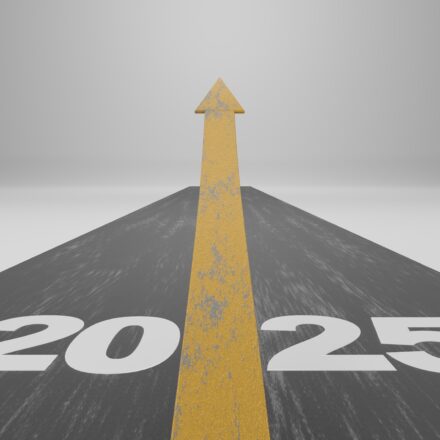
Learning Zone
2025 Fleet Trends: What’s Shaping the Future of Fleet Management?
Read more
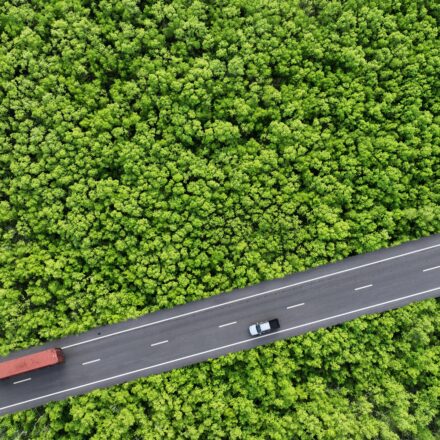
Learning Zone
Webinar: Driving Sustainability – Green Fleet Management Trends For 2025
Read more
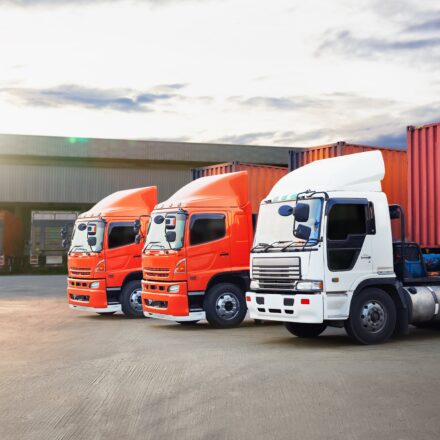
Learning Zone
Navigating Insurance in the Fleet Industry: Tips and Trends
Read more

Learning Zone
The Role of AI in Predictive Maintenance
Read more
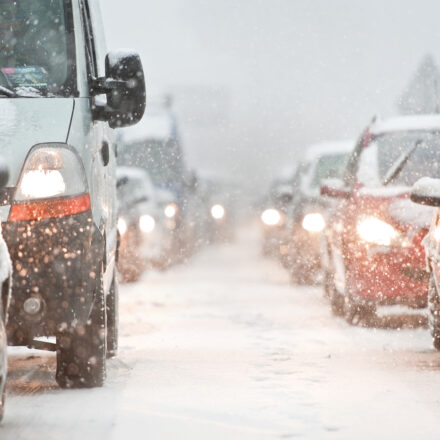
Learning Zone
How to Prepare Your Fleet for Winter: A Comprehensive Guide
Read more
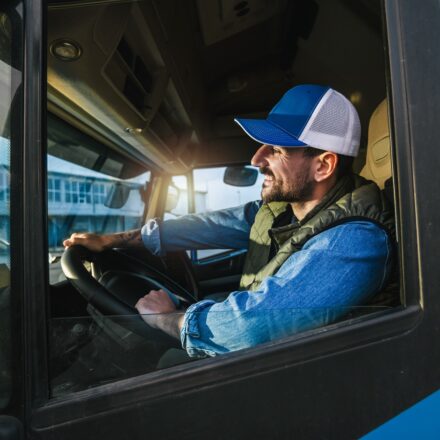
Learning Zone
Driver Shortages and Retention: Strategies for Fleet Managers
Read more
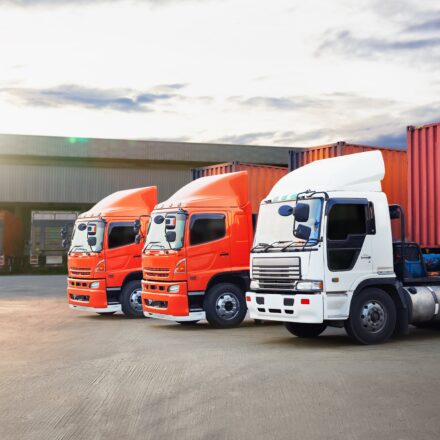
Learning Zone
Streamlining Truck Fleet Management: How Technology Can Overcome Industry Challenges
Read more
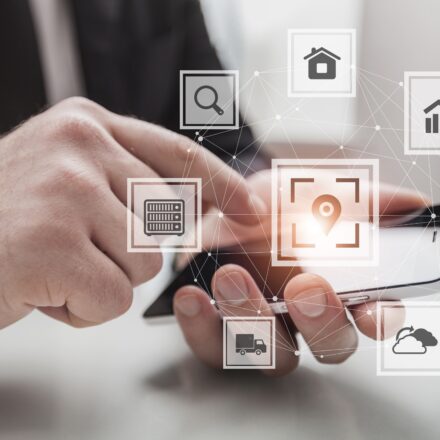
Learning Zone
How to Boost Productivity with Fleet Management Automations
Read more
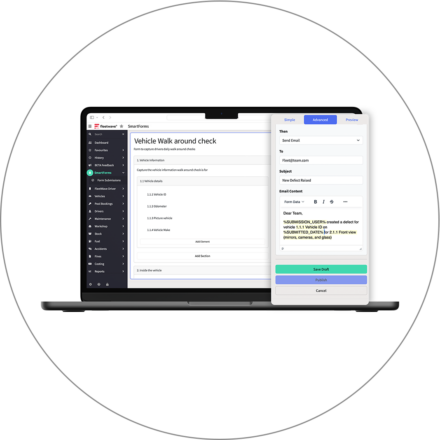
Learning Zone
Webinar: Innovation Through Automation – Make your Fleet Smarter
Read more
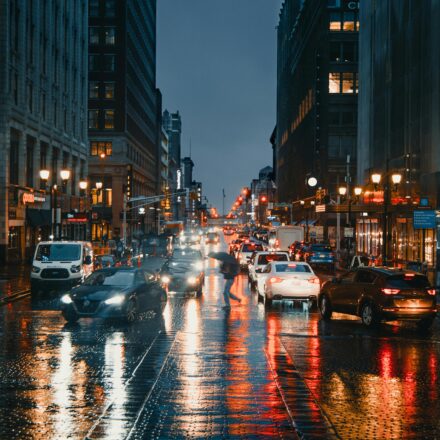
Learning Zone
Mastering Transportation Challenges: Leveraging Fleet Management Software for Optimal Solutions
Read more
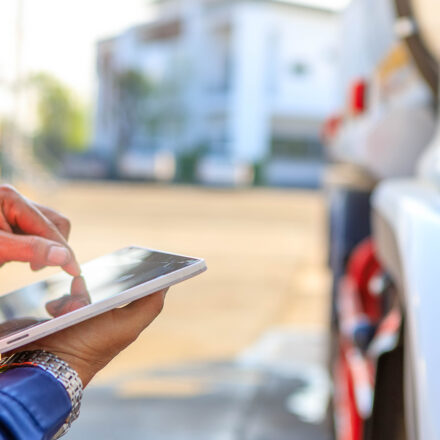
Learning Zone
The Advantages of Digital Forms over Paper Forms in Fleet Management
Read more
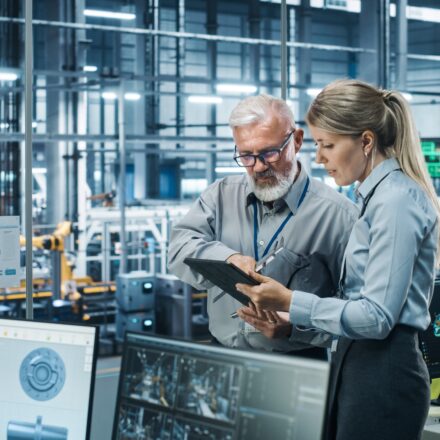
Learning Zone
How Software helps Manufacturers better manage their Fleets
Read more
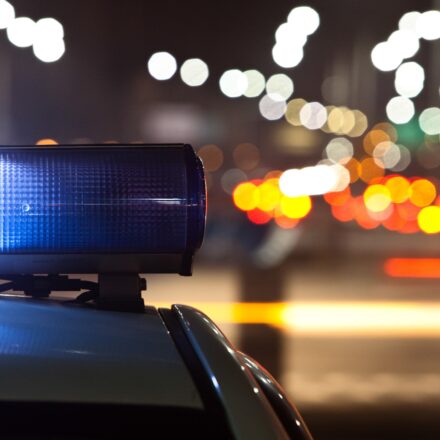
Learning Zone
The Benefits of Fleet Management Software for Government Fleets
Read more
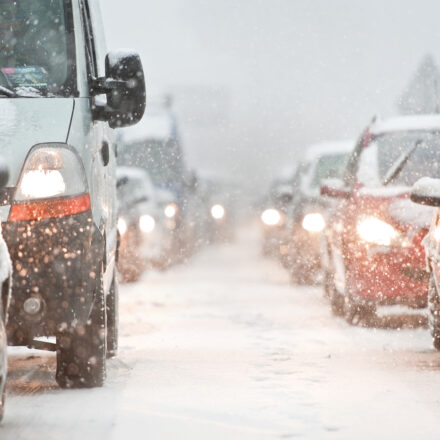
Learning Zone
Webinar: Preparing your Fleet for Winter: Essential Tips and Strategies
Read more
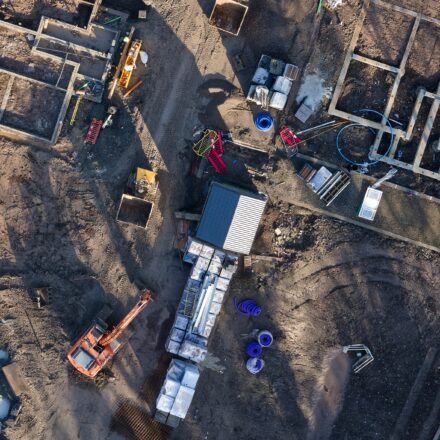
Learning Zone
Webinar: How to Create an Effective Fleet Asset Management Plan
Read more
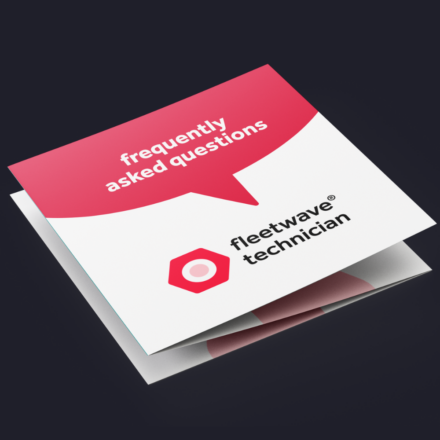
Learning Zone
FleetWave Technician FAQ’s
Read more
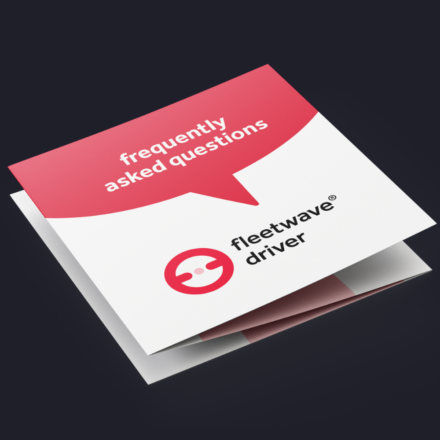
Learning Zone
FleetWave Driver FAQ’s
Read more
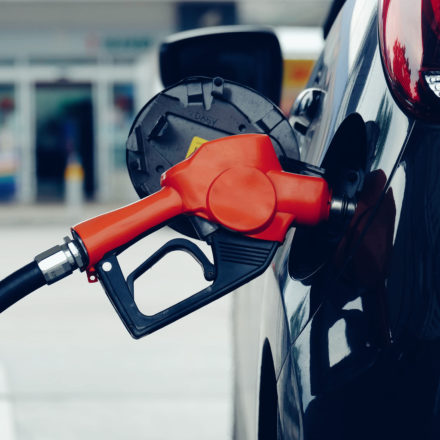
Learning Zone
Webinar: 6 Ways to Save on Fleet Fuel Costs
Read more
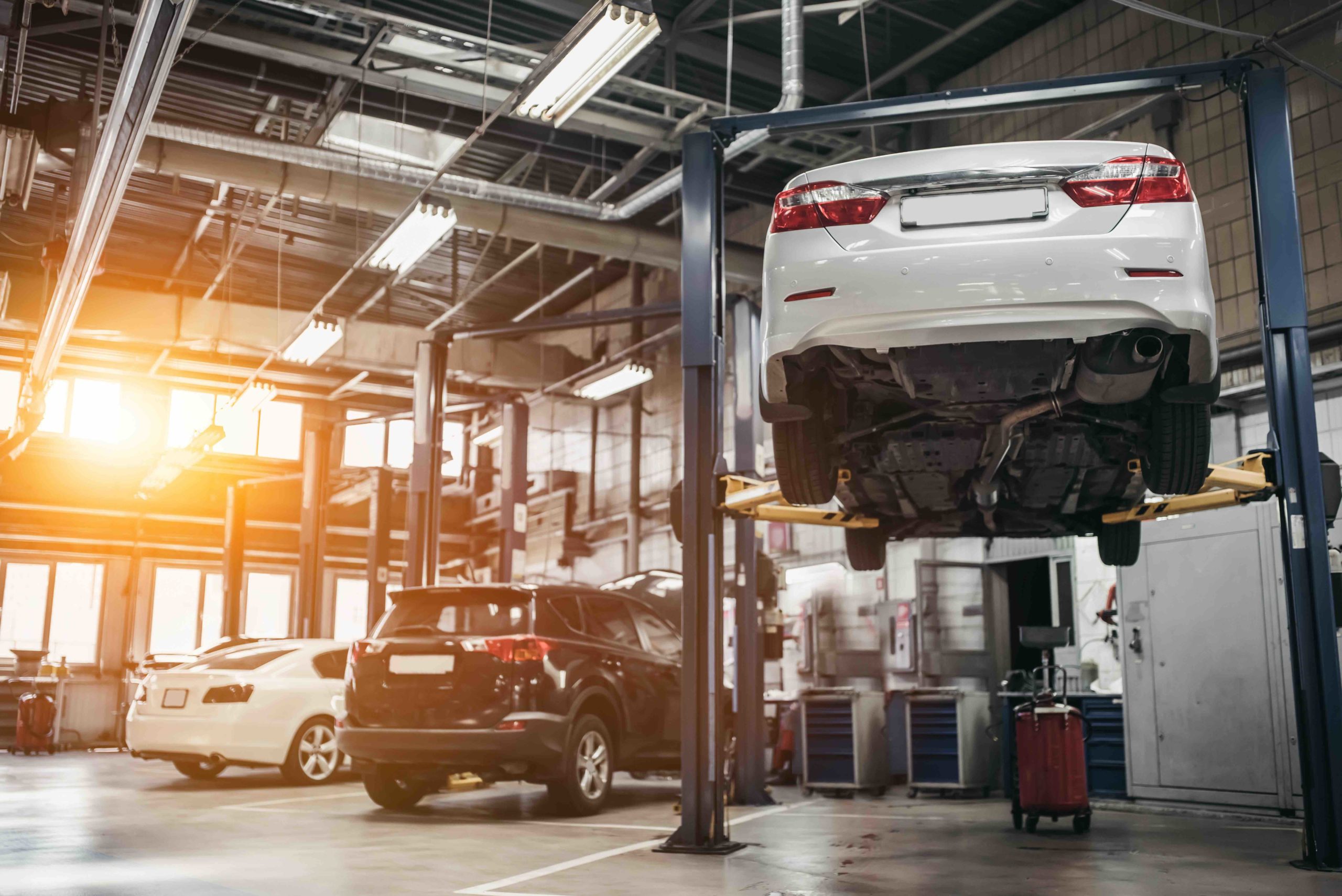
Learning Zone
Webinar: Unchained Maintenance – How Better Fleet Maintenance Relieves Supply Chain Headaches
Read more
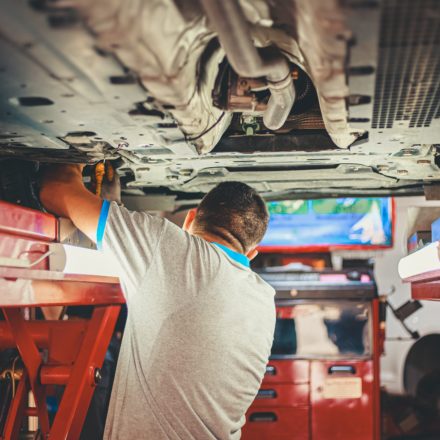
Learning Zone
How mobile apps can improve your fleet workshop
Read more
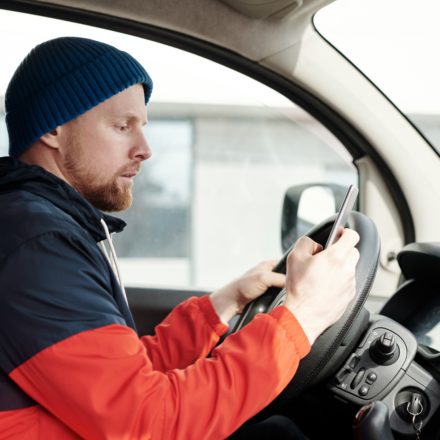
Learning Zone
The importance of mobile apps for fleet drivers
Read more
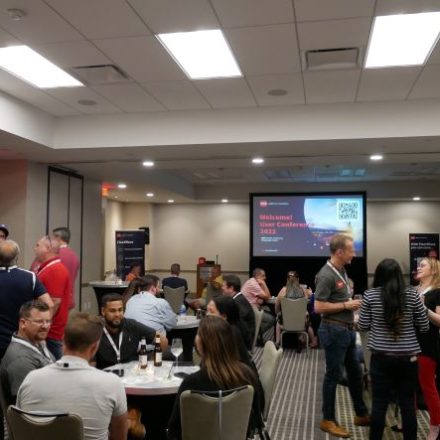
Learning Zone
Chevin Annual Conference 2022
Read more
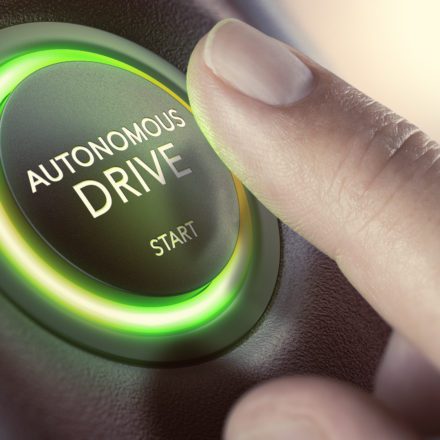
Learning Zone
Autonomous Cars Guide for Fleets
Read more
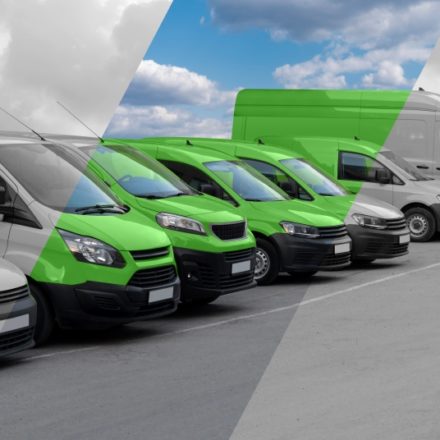
Learning Zone
Green Fleet Management
Read more
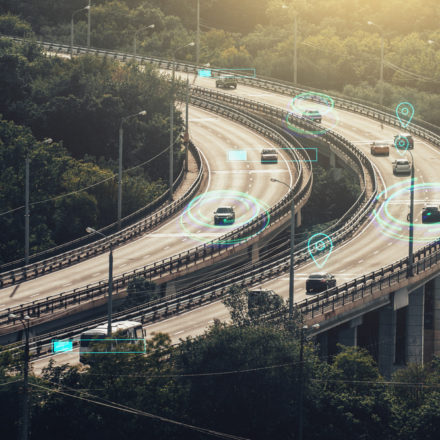
Learning Zone
The Importance of Automated Fleet Solutions
Read more
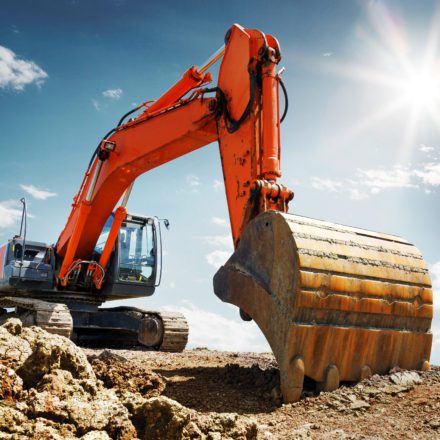
Learning Zone
Fleet Management Software for Construction
Read more
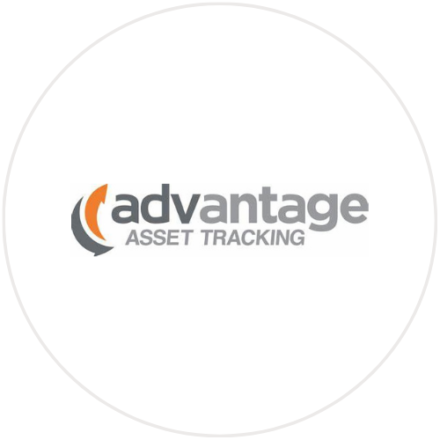
Learning Zone
Webinar: The Power of Combining Telematics with Fleet Management
Read more