Learning Zone
How to Reduce Fleet Downtime?
In today’s competitive business landscape, managing fleet downtime is crucial for maintaining operational efficiency and profitability. Unplanned vehicle breakdowns not only lead to substantial costs but also hinder your ability to meet customer demands and capitalize on opportunities.
For many company fleets, downtime is tangible and can be translated into dollars. In fact, downtime costs a fleet an average of $696 to $1,181 a day, per vehicle, and those figures add up fast.
For example, a 1,000-unit fleet with an average of five 90-minute downtime events per unit, per year, will result in an annual downtime cost of nearly 1 million dollars; $925,305 to be exact. That is a substantial cost, some of which is avoidable.
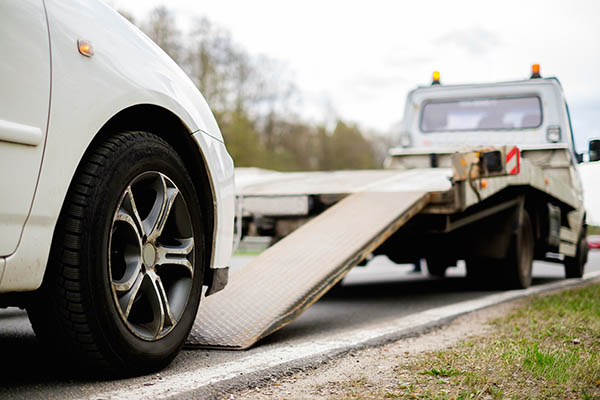
In this blog, we will explore 6 effective strategies to reduce downtime and enhance fleet productivity.
1. Choosing the Right Vehicles:
Selecting the appropriate fleet vehicles is the foundation for minimizing downtime. Outdated or unfit vehicles are more prone to wear and tear, resulting in costly breakdowns. While replacing vehicles involves a capital investment, the long-term benefits outweigh the initial cost. Newer vehicles equipped with advanced technology are less likely to experience unplanned service events.
2. Conducting Comprehensive Inspections:
Implementing a rigorous fleet inspection process is essential for identifying issues before they escalate into downtime-causing problems. Utilizing on-board telematics systems to monitor fault codes and alerts enables timely intervention. Addressing minor issues promptly prevents them from developing into major repairs, reducing overall downtime.
3. Implementing Proactive Preventive Maintenance:
A proactive preventive maintenance (PM) program is instrumental in minimizing downtime. Regular maintenance schedules keep vehicles in optimal condition, preventing breakdowns. Including a component replacement plan based on expected life cycles further reduces the risk of sudden failures. Scheduling maintenance during off-hours minimizes the impact on operations.
4. Streamlining Workshop Management:
Efficient workshop management is crucial for reducing downtime. Often, downtime is not caused by repairs themselves but by inefficient service processes. Collaboration between maintenance, operations, dispatch, and administrative teams is essential. Proper resource allocation and process optimization eliminate backlogs and enhance overall efficiency.
5. Driver Training and Skill Development:
Investing in driver training pays off by reducing avoidable breakdowns. Well-trained drivers are better equipped to operate vehicles properly, preventing unnecessary wear and tear. Additionally, skilled drivers are less likely to be involved in accidents, further minimizing downtime due to collisions.
6. Leveraging Fleet Management Software:
Fleet management software is a powerful tool for maintaining fleet efficiency. It aids in managing inspections, preventive maintenance programs, and driver operations. By analyzing fleet data, the software predicts recurring issues, enabling proactive measures to prevent future downtime.
By implementing these strategies, your fleet can operate with minimal disruptions, leading to increased productivity, improved customer satisfaction, and sustained business success.