Learning Zone
How to run an efficient Fleet Workshop
Four top tips to improve workshop efficiency
If your company views an in-house fleet workshop as a necessary business cost, it may be time to re-think that approach.
A well-run workshop not only supports your fleet operation though servicing and maintenance, it could also be a revenue generator.
Some of our customers use their workshops to provide contract maintenance services to external customers. If you already run a workshop there are a number of potential gains to be made by taking steps to improve its efficiency – including reduced costs and downtime.
So how exactly do you improve workshop efficiency?
Read on for some simple tips…
1. Improve scheduling
Make sure your workshop runs as close to full utilisation as possible. While it’s important to ensure that you aren’t left waiting for stock to come in; having excess or obsolete stock can prove very costly.
Understanding how your assets are used and replenished is the first step in creating more appropriate scheduling for your operation and helping ensure your workshop is well-utilised both now and in the future.
We think it’s important to take a range of factors into account, such as:
- Inventory turnover
- Real-time parts availability
- Usage trends and forecasts
- Replenishment time
- … and more
Make sure that these factors are assessed on a regular basis, as this will help you identify any new trends or issues as soon as they occur. The need for effective scheduling also applies to staff utilisation, which brings us to our next point….
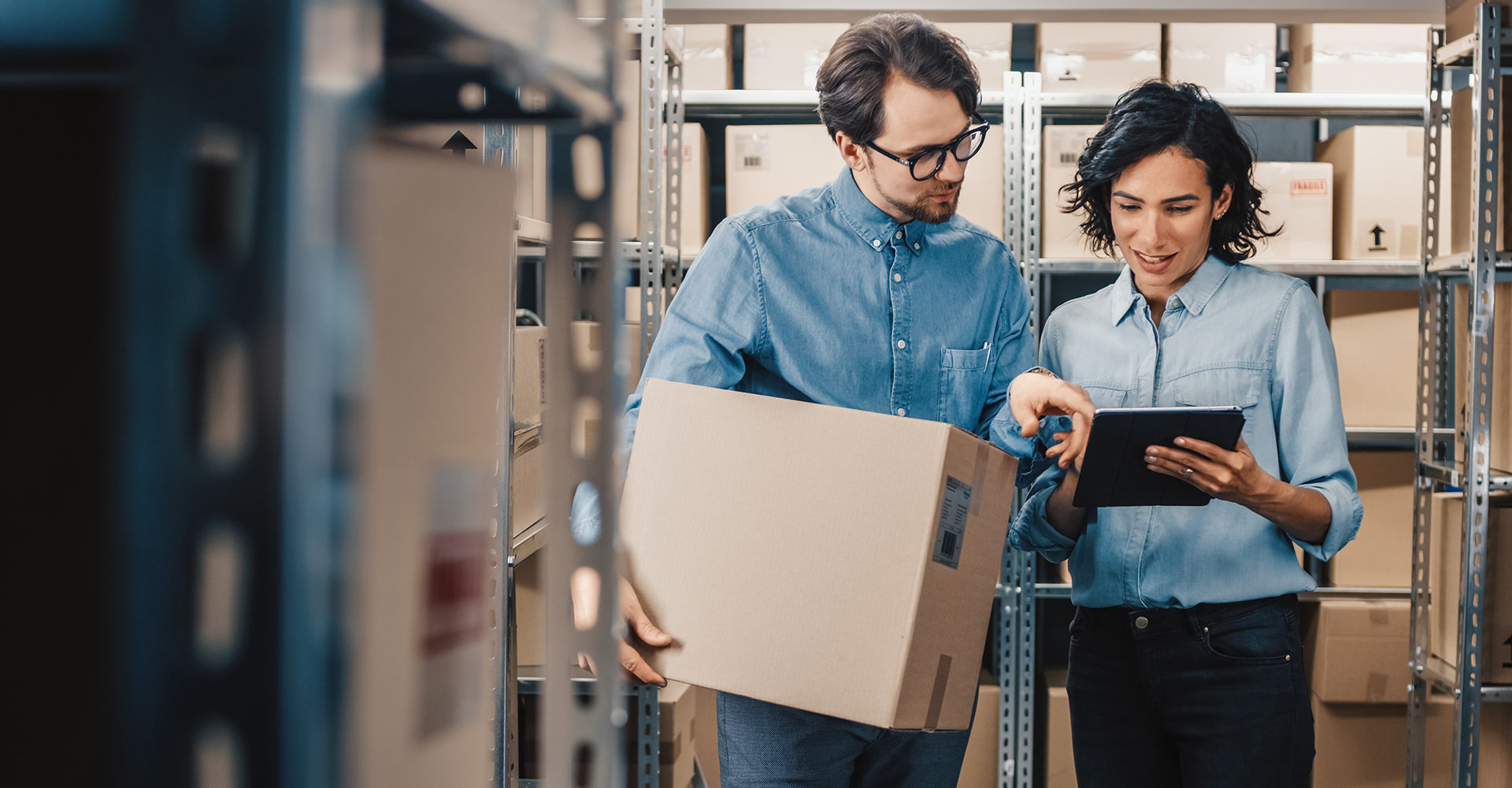
2. Improve staff planning
It’s a somewhat clichéd phrase, but your staff are probably the most expensive resource in your workshop, so it’s vital that you make sure your technicians are managed effectively.
This means having procedures in place for sick days, holidays and other absences to minimise disruption. You should also understand your team’s availability and training levels and plan well ahead by cross-referencing staffing against forecast requirements.
We suggest you look carefully at your fleet’s maintenance needs too – it could be that some works are seasonal, or they are affected by recalls and campaigns, so take steps to increase your knowledge of such trends.
3. Improve job card management
Your technicians will perform more efficiently if they know exactly what they should be doing to which vehicle and when. Industry standard repair times can also be utilised to support job creation and implementation.
When creating job cards, you should also take steps to ensure that all the information required is easily available. If a technician is not able to easily view or understand job requirements, it could result in increased job times and costs, and reduced compliance.
4. Improve visibility
Our most important tip is to make sure you understand what is available in your operation at all times. If you can’t measure it, you can’t manage it, so take steps to improve the visibility of your assets.
This is a process that starts from the bottom up: you need to have a solid overview of everything from service histories, maintenance schedules, parts inventory and warranty coverage through to workshop equipment, technicians (and their capabilities) and vehicles.
Make sure you:
1. Take time to research how you track and measure asset availability, jobs and costs.
2. Assess how your processes could be improved. Be honest with yourself – are you able to track and measure all costs associated with a vehicle, maintenance schedule or repair event? If a part was needed, could it be easily located? Time is money, so the longer team members spend looking for items the more costly jobs become.
3. Understand where improvements can be made so that you can take steps to fix problems.
How software can help
We know from our clients that managing and monitoring workshop activity is easier and more efficient when you use workshop management software. The improved visibility of maintenance schedules and technician availability helps to increase workshop productivity.