Learning Zone
The right parts at the right time
Five ways inventory management can create a successful fleet workshop.
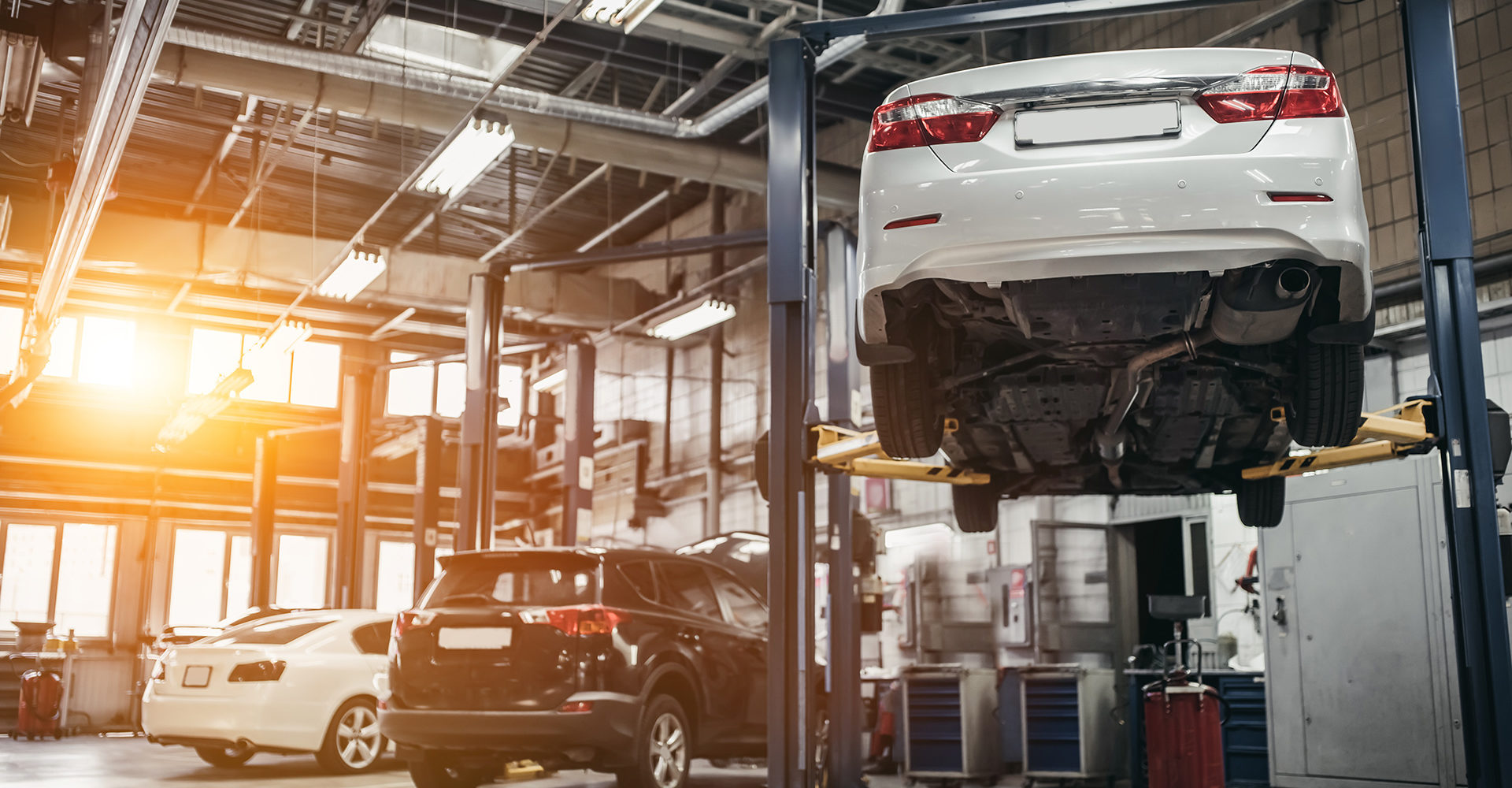
It has been well-documented that as vehicle complexity increases the costs of parts, and often repair, has risen. But that doesn’t mean you should accept that service, maintenance and repair (SMR) will always be a growing area of expenditure. You can mitigate against these costs by making more efficient repairs and avoiding the cost implications of vehicle downtime.
You can significantly streamline your operation by getting your inventory management and supply right. And you‘ll save time and money in the process. Here’s how: https://www.automotive-fleet.com/348040/vehicle-complexity-increasing-fleet-repair-costs
Best Practice #1 – Stay organised
Ask yourself:
- Do my technicians know where parts can be located?
- Can frequently used parts be accessed quickly to keep workshop operations running smoothly?
If the answer is no, or a little vague, then there’s work to be done. But don’t panic – organising parts so that fast-moving items (such as those used in servicing), can be found quickly can be fairly straightforward.
Get your important parts up front. Shelves and storage areas need to be arranged so that components for major system categories such as engines, brakes and electrics can be pulled at a moment’s notice.
Often workshops devote too little time to proper stock planning. Taking the time to implement a slick inventory management system will allow your workshop manager to accurately allocate time for jobs, so you’ll find out where the bottlenecks are, or what vehicles take too much time to repair.
Best Practice #2 – Develop parts knowledge
Identify the parts that get used a lot, and those that do not. There’s nothing more frustrating than having a service or repair delayed because the right parts are not on hand. The depth of your inventory and the way that it is managed are critical success factors in having the right parts available, when and where they are needed.
Also, having a high inventory of a particular part that is rarely needed is wasteful. It’s unnecessary expenditure and, ultimately, takes up storage space that could be better utilised.
Inventory control staff require a good working knowledge of vehicles and their parts requirements. Knowing that particular vehicles follow a parts replacement cycle allows for efficient planning, and far more cost-effective purchasing practices. It also ensures stock is on hand, so that last-minute and expensive parts ordering is kept to a minimum.
Service data from telematics systems can provide you with the information that will enhance your inventory optimisation plan, further reducing downtime from service.
Best Practice #3 – Integrate your management systems
Connect the dots. It’s important to look at how your fleet management and other software systems work together. Integration also ensures data accuracy and reduces demands on administrative, finance and other personnel.
Monitor and adjust stock based on usage and planned upcoming needs using smart, adaptable fleet management software. Information on parts used can be seamlessly transferred from repair orders to a central system, so purchase orders can be automatically issued when stock levels drop to a pre-determined level.
You’ll be able to use valuable data on parts failures and items that are not lasting for their expected service life using these integrated systems, so you can make more informed purchasing decisions about vehicles and parts.
Best Practice #4 – Make vendors a resource
Suppliers’ expertise is there to be used. Most would be happy to help with your inventory management because it will mean them working more closely with you.
Their experience across many fleets can help identify recommended maintenance schedules to prevent failures and compare parts from different manufacturers.
With a wider view of the market, your suppliers can also determine which parts provide your operation with the best overall value. That knowledge and experience is the source of finding not just the lowest prices, but also the right parts at the lowest cost.
Increasingly, parts suppliers are making it possible to integrate their inventory and purchasing systems with your fleet and asset management solutions. That connection can be very effective for handling emergency parts orders and in tracking warranty coverage on replacement parts, making it easier to make a claim if necessary.
Best Practice #5 – Utilise inventory management software
Parts are getting more complex and numerous. Using software to manage them is crucial.
Inventory levels can be monitored and adjusted remotely, based on usage and upcoming needs. Everyone can see what is stocked, and where.
Eliminating paper-based and manual processes, fleet and asset management software will streamline administrative and management practices.
With a parts inventory management system in place, your fleet’s shop and technician productivity can rise, boosting asset utilisation by returning vehicles to service faster.