Learning Zone
5 Ways to Reduce Fleet Maintenance Costs
As fleet maintenance costs continue their upward trajectory, the industry faces a pressing challenge. Newer equipment comes with heftier price tags for repairs and maintenance, contributing to the escalating expenses. Furthermore, the constant struggle to attract and retain skilled maintenance technicians adds to the strain on labor costs.
The complexity of fleet maintenance costs lies in their variability, influenced by a myriad of factors. Your operational assets, part and supply expenses, warranty coverage, and even external factors like road conditions and weather all play a role. Despite these challenges, conquering fleet maintenance costs is far from impossible.
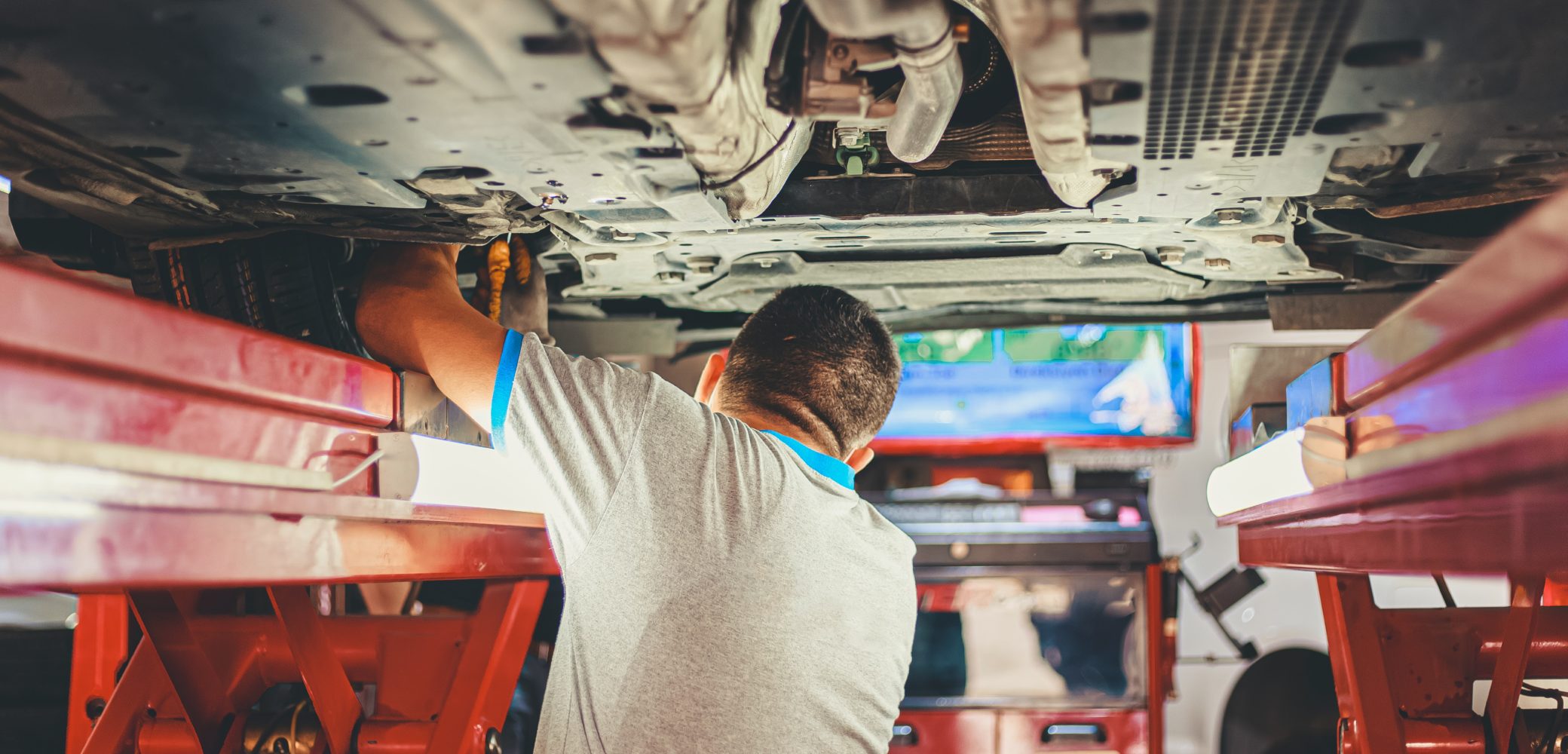
In this blog, we’ll explore five strategies to help you reduce fleet maintenance costs, increase efficiency, and maintain a competitive edge:
1. Proactive Planning
Proactive planning serves as a powerful tool to curtail fleet maintenance costs. By forecasting maintenance needs and strategically scheduling tasks, businesses can effectively prevent costly breakdowns and minimize unplanned downtime.
This approach enables the timely acquisition of necessary parts and efficient allocation of workforce resources, optimizing repair processes. Moreover, preventive measures taken during scheduled maintenance intervals can identify and address potential issues before they escalate, resulting in less intricate and more cost-effective repairs.
Proactive planning not only enhances operational continuity but also translates to reduced emergency expenses, improved equipment longevity, and ultimately, substantial savings in fleet maintenance expenditures.
2. Parts Inventory Management
By strategically placing essential components in accessible locations, you ensure that technicians can efficiently carry out service and repair tasks, reducing labor expenses. This streamlined approach not only minimizes downtime but also increases vehicle uptime, as well-maintained inventory eliminates unnecessary delays.
Prioritizing frequently used parts and trimming rarely needed items from your stock further refines the process, saving both time and resources. Leveraging data-driven insights and strong supplier relationships enables accurate demand forecasting and quicker access to components. Centralized tracking through inventory management software empowers informed decision-making, bolstering your fleet’s overall maintenance efficiency.
Best practices for optimizing parts inventory
3. Optimize Maintenance Approach: In-House vs. Outsourcing
Choosing the right approach to fleet maintenance can significantly impact your costs. Evaluate the pros and cons of managing maintenance in-house versus outsourcing it to specialists. In-house management offers greater control over costs, quality, and scheduling, while outsourcing provides access to trained technicians, pre-agreed maintenance costs, and reduced capital investment. Striking the right balance between the two approaches can lead to substantial cost savings.
4. Create Well-Defined Fleet Maintenance Programs
The adage “planning prevents poor performance” holds true for fleet maintenance. Establish clear and comprehensive maintenance schedules that include routine service intervals, checklists, and detailed instructions. Leverage data from telematics systems and driver reports to inform your maintenance program. By sticking to these schedules, you can predict costs more accurately, lower labor expenses, and improve overall workshop productivity.
How to create an effective fleet maintenance program
5. Leverage Technology for Data-Driven Insights
In today’s digital age, technology can be your greatest ally in reducing fleet maintenance costs. Implement fleet maintenance software that provides valuable data insights. Analyze this data to identify areas for improvement and cost-saving opportunities. By harnessing technology’s power, you can streamline operations, enhance efficiency, and make informed decisions that positively impact your bottom line.
Conclusion
Reducing fleet maintenance costs requires a strategic and holistic approach. By embracing proactive planning, optimizing maintenance approaches, creating well-defined programs, and leveraging technology, you can take significant steps toward cost reduction and operational efficiency.
Remember, each cost-saving measure contributes to your overall success, enhancing your reputation, profitability, and long-term growth prospects.