Learning Zone
Managing your inventory
Controlling parts and stock levels is an important part of fleet management and is integral in successful inventory management.
We look at the proven approaches to having an effective parts management plan.
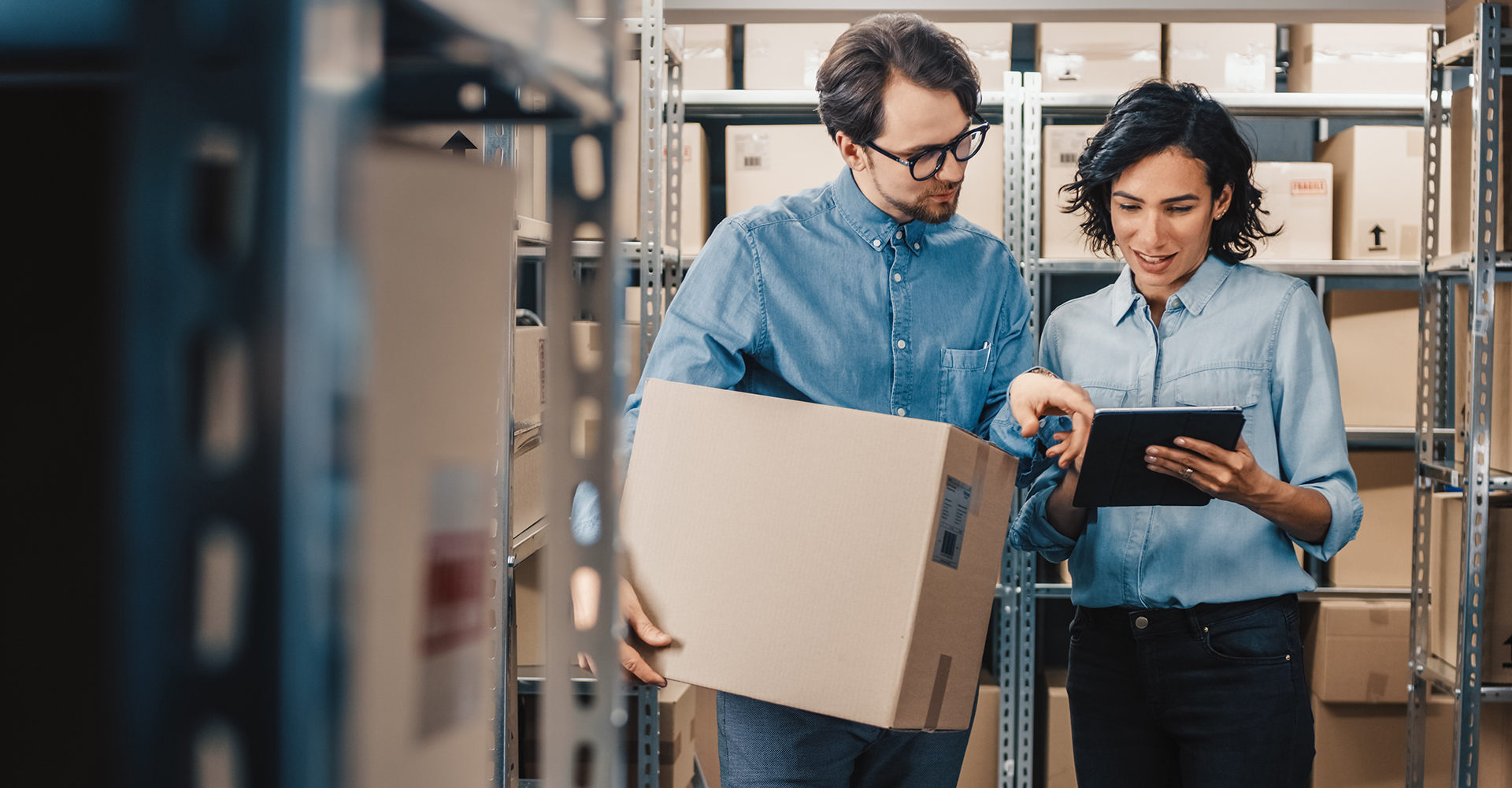
Having good inventory management processes saves time and money in several ways. With the average cost of trucking maintenance and repairs increasing every year, addressing inventory management practices can reduce the risk of additional, unnecessary spend that may have been better used in other areas of your operation.
Inventory management isn’t just about cost, however – it’s also about profitability. Eliminating poor inventory management with an effective strategy will always have a positive impact on a fleets’ bottom line.
You can also increase productivity through reduced downtime, which will have a positive effect on meeting customer service and satisfaction levels.
Five things good inventory management will stop:
- Rising part costs due to a lack of visibility and control over inventories.
- Reduced shop productivity through unnecessary time spent searching for parts.
- Lower warranty recovery due to an inability to track coverage, leading to missed claims.
- Reduced asset utilization due to time spent searching for parts which increases downtime.
- Declining customer satisfaction through delays to the delivery of goods and services.
Putting simple practices in place:
If managing thousands of parts and spares all seems too complex, don’t worry. It’s not. It’s relatively easy to find solutions to streamline inventory management practices.
Follow these 5 tactical approaches to optimize you inventory management:
1. Organize your parts room
When frequently used inventory is easy to access, shop technicians can become more productive. Arranging inventory on shelves and bins so that components associated with systems, such as brakes and electrical items, can be located helps staff fill repair needs quickly. Good parts room housekeeping also helps identify slow-moving and obsolete parts that take up limited shelf space and raise inventory costs.
2. Improve visibility of parts
Nothing reduces asset utilization and impacts on customer service more than having maintenance or repair jobs delayed because the right parts are not in stock. By addressing poor inventory management problems, the correct items and parts quantities are always available to meet maintenance and repair needs. Efficient inventory planning also promotes effective purchasing practices, reducing the need for those costly last-minute orders.
3. Train technicians
When parts staff and technicians have the knowledge to recognize which parts are fast moving and need to be re-ordered more frequently, inventory needs can be met more effectively. Incorporating parts inventory topics into in-house training programs can help develop these skills. Parts management training programs are often available from industry associations – The National Institute for Automotive Service Excellence (ASE) offers a certification program for parts specialists, for example.
4. Utilize vendor resources
Parts suppliers have information that can help predict parts needs, helping you establish effective ordering parameters. Along with details of your fleet’s previous purchases, an industry-wide view of parts usage can help compare quality, service life and costs among manufacturers. Parts vendors can provide integrations with purchasing systems that automate ordering – useful for when an emergency parts order is needed!
Streamline inventory with software
There are numerous measurable benefits that come from using a parts inventory management system as part of an advanced fleet and asset information solution:
Automated inventory replenishment
Minimize time-consuming administrative tasks through automated replenishment so parts can be stocked based on usage and upcoming needs. Software can also automate the purchase order process using predetermined parameters.
It can ensure accuracy and reduce management time by seamlessly and automatically transferring parts information from repair orders for internal billing and for vendor returns and payments through integration of your software across all departments.
You can also use fleet software to discover data and trends about failures and usage, which will enable you to make much more informed vehicle, equipment and replacement parts purchasing decisions.